Main Field(s) of Science / Technology
Developments and advancements in Electrical Engineering and, most notably, improvements in the speed, efficiency and cost-effectiveness of installation processes, with particular emphasis on medical grade buildings and facilities.
Baseline Scientific / Technological Knowledge
Existing practice and experience in the market prior to the Covid-19 pandemic was for improvements to medical grade facilities to be undertaken slowly and carefully, with new and improved systems & components installed and trialled in several stages.
Once the pandemic had begun, it was clear this approach would no longer be appropriate. However, just going at it like a “bull in a china shop” was not advisable either, as mistakes would undoubtedly be made, which could lead – ultimately – to loss of life. Thus, development of a rapid response process that could be rolled out immediately was necessary.
BoJen were approached by Oxford University Hospitals and the NHS to convert an old 1960’s hospital building into a new top grade infectious diseases trials unit facility as quickly as possible. The Company were provided only with a 12-page brief and performance specifications. Rapidly converting such basic requirements into a full-blown scheme to develop and install multiple complex systems is not something that was standard practice, nor was there any practical information on how to do it freely available in the public domain.
BoJen were trusted with this critical undertaking due to their considerable technical expertise and their renowned ability to deliver complex projects on time and within budget. The ability to “think outside the box” and devise innovative solutions was key.
Scientific and Technological Advance
To develop systems and processes to allow for conversion of old and outdated medical premises into top grade, state-of-the-art facilities that can be used to study and treat infectious diseases. Specific requirements included development and installation of all the latest technologies in infectious disease control, air extraction systems with specially designed ventilation generator back-up, specialised lighting and controls for clinical spaces and overnight stay rooms. Additionally, security, door access and intercom/panic systems were required.
Key areas for development included:
- Creating negative pressure in rooms to ensure air leakage (and potential cross-contamination) is insignificant to adjoining areas.
- Tuneable lighting, controlled via scene select controllers, linked to main room controls, to allow different light colour variances, e.g. to enable veins to be seen easily.
- Devising an efficient and effective design concept to link multiple divergent systems through a main control room, including monitoring systems, patient CCTV, intercoms, alarms, access controls, etc.
- Design of an efficient and robust generator system as a back-up for all critical services. A key element to the advances sought was to achieve development and installation / deployment within a short timeframe and to tight financial budgets.
Scientific and Technological Uncertainties
There were several significant challenges that the Company had to overcome. for example, the large electrical output required for the back-up generator created issues with: the sheer size of the unit and how to enclose it safely and effectively; solving acoustic problems, i.e. reducing noise. This was a particularly vexing problem as the site positioning was restricted by severe planning requirements, decibel levels had to be minimal due to local area noise constraints – especially as new NHS staff accommodation buildings were to be sited directly adjacent to the generator site.
The project required installation of medical gas and power points in clinical spaces, in the middle of the rooms. This required development of a retractable column pendant supported from the ceiling. Issues with vibration during operation and the sheer weight of the pendant meant that additional supports needed to be designed. A further issue was that standard installation – by cutting into the ceiling – was not practical or possible, thus requiring further design adaptations.
The tuneable lights were to be controlled via an App-controlled addressable system that had not been used before. There was incompatibility between the various components, creating power supply issues, which had to be rectified. This also required on-site modifications to the overall installation.
Overcoming the Uncertainties
This ongoing project commenced at the end of 2020. In the previous period the Company managed to devise processes and procedures that would – hopefully – allow for rapid deployment of the full system, once devised, and tested. This first phase was critical to allow for completion within a very short timeframe and was ultimately successful.
In the 2021/22 period, work focused on developing components and systems to achieve the very exacting specifications set. Prototype components developed included:
- Fixings and cowlings for the retractable pendants. This included modifications to allow the semi-recessed units to sit flush with the ceiling (to reduce the risk of contamination); and devising a cowling to adequately protect all connections to the power data and medical gases.
- The tuneable lighting needed significant adaptation to achieve the specifications required. This involved the BoJen team “breaking in” to the wiring systems to create connection units with din rail mounted ELV power supply connections inside an enclosure and modifying the wiring problems in trying to link the lighting to the App controlled addressable system and including all the additional functionality required. Problems included the lights operating ‘of their own accord’ on occasions in the middle of the night, waking trials patients from their sleep.
Ultimately, the project was a success, with commissioning occurring at the end of October 2021. However, BoJen continued to monitor the systems to ensure all aspects performed as expected. Some further improvements were necessary on the tuneable lighting to resolve ongoing issues.
BoJen are very happy to have devised this new process (and system adaptations), which can now be marketed to others as and when the need for rapid deployment of medical grade facilities arises.
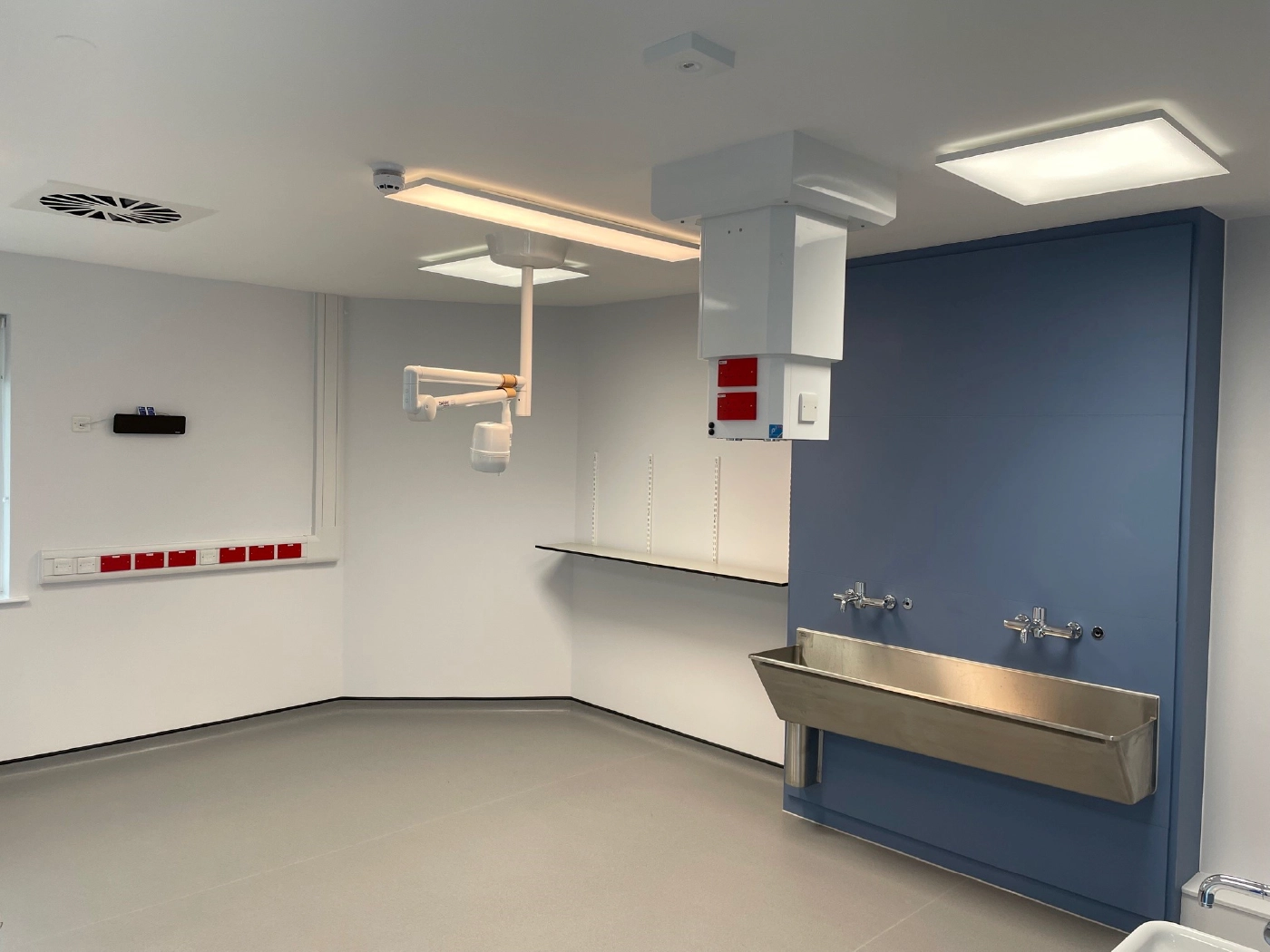
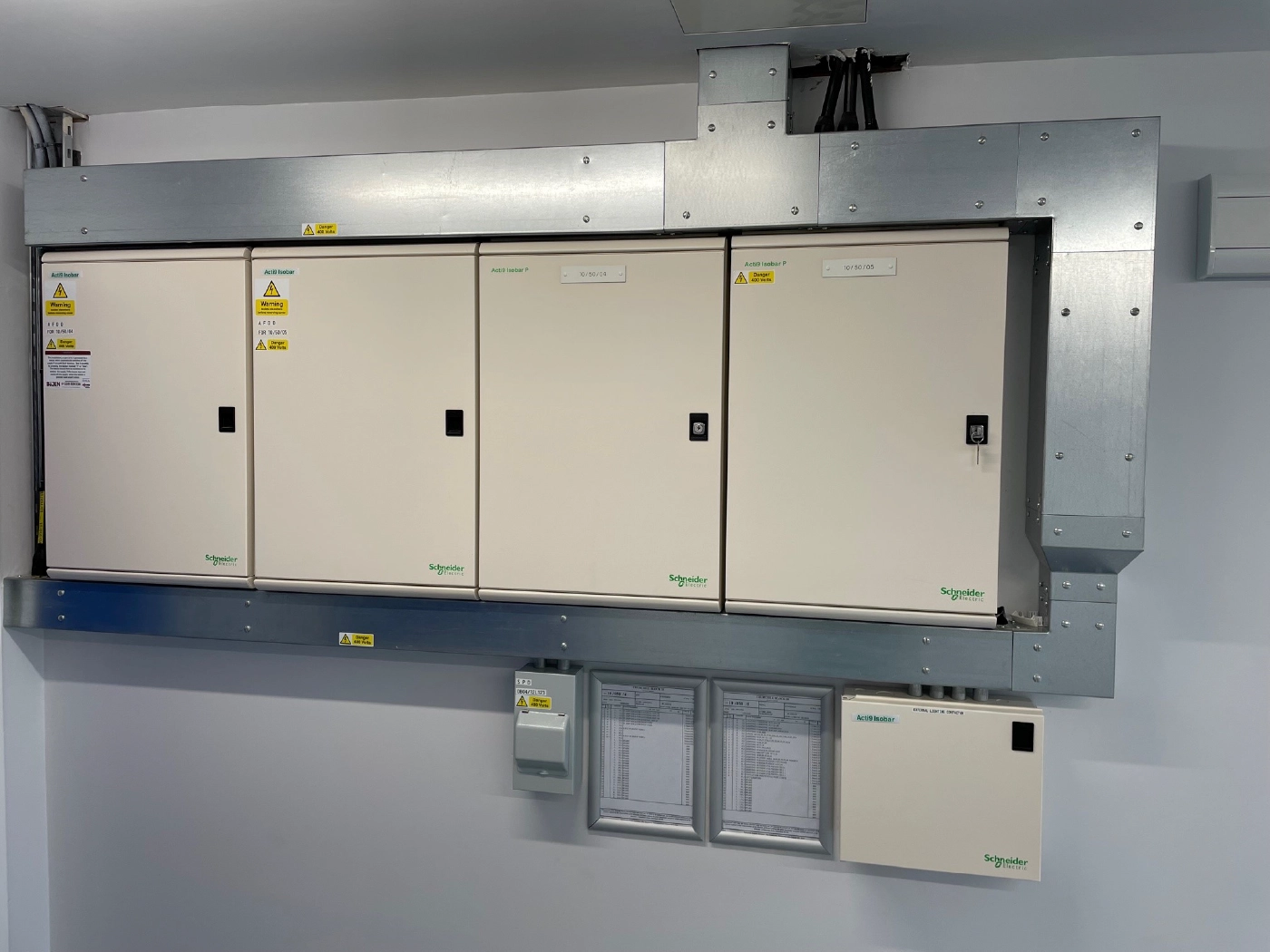